Your challenges
Water treatment facilities today face complex demands. CeraMac® helps you respond to these challenges:

Anticipate Upcoming Regulation
Meet increasingly stringent regulatory requirements, including 4.0-log removal of pathogens like Cryptosporidium and Giardia, and consistent turbidity control.
Protect People's Health
Provide a strong and durable barrier against pathogens and contaminants, even with fluctuating source water quality.
Protect the Water Resource
Reduce chemical use and extend treatment asset life with a robust and easy-to-clean membrane system.
Reduce Carbon Footprint
Benefit from a low-energy, long-life filtration system with minimal waste.
Resilience to Climate Change
Perform reliably under variable water conditions and during extreme weather events.
Optimize TOTEX
Reduce both capital and operational expenses through low maintenance needs, long membrane life, and high productivity.
Do you want to know more about CeraMac® membrane filtration system?
How does it work ?
Water passes through the porous ceramic membranes, effectively removing turbidity, particulates, pathogens, and other suspended contaminants.
All feed water becomes filtrate, minimizing waste and maximizing yield.
To enhance performance, especially for the removal of organic matter and micropollutants, CeraMac® can be combined with ILCA – In-Line Coagulation and Adsorption. ILCA acts as a pre-treatment step, significantly improving removal efficiencies and extending membrane life. This combination offers a powerful, low-footprint solution for advanced drinking water treatment.
Backwashes & Cleaning
An integrated automated backwash system cleans the membranes using high-pressure water (up to 5 bar) flowing in reverse direction (from permeate to feed), often assisted by an air-spring. This quick process lasts only a few seconds and helps maintain membrane performance and reduce fouling.
For more intensive cleaning, optional processes can be applied:
- Chemically Enhanced Backwash (CEB or EBW): short cleaning cycles using sodium hypochlorite, hydrogen peroxide/acid, or ozone, typically lasting around 10 minutes.
- Clean-in-Place (CIP): full chemical cleaning using chlorine-based, low-pH/peroxide, or ozone-based methods. The frequency of CIP depends on the fouling rate and feed water quality.
Membrane Integrity Test (MIT)
The integrity of each membrane vessel is continuously monitored through an automated Membrane Integrity Test (MIT). These tests are programmed to run daily or at user-defined intervals (e.g., every 24 to 168 hours) and are designed to detect any physical or performance-related issues, ensuring safe and reliable operation over time.
Configuration Options
CeraMac® is available in multiple vessel sizes to meet a range of flow and footprint requirements:
Model | Number of Membranes | Filtration Surface Area |
C8 | 8 | 200 m² |
C19 | 19 | 475 m² |
C37 | 37 | 925 m² |
C90 | 90 | 2,250 m² |
These modular configurations support scalability and are suitable for both greenfield installations and retrofitting existing plants, offering flexibility in plant design and expansion.
Our positive impact
CeraMac® addresses today's water treatment challenges with a robust, sustainable, and efficient membrane solution:


Enhanced Water Quality
Delivers high-quality treated water by effectively removing turbidity, pathogens such as Giardia and Cryptosporidium, and other contaminants, even under variable source water conditions.

Modular Design
Modular, frame-based construction enables substantial parts of the works to be completed off-site, accelerating installation, reducing environmental disruption on-site, and allowing easy scaling up.

Sustainability & Carbon Footprint
Made from durable, fully recyclable materials with no plastics. Our ceramic membranes have a proven service life of over 20 years in continuous operation. Both the membranes and system components are designed to minimise environmental impact over their lifecycle. The system also supports a reduced carbon footprint through low energy consumption and limited chemical usage compared to traditional technologies.

High Reliability & Efficiency
Achieves high throughput with a compact system footprint and low energy requirements. CeraMac® is resistant to fouling and compatible with strong cleaning agents, including ozone, ensuring stable performance with minimal downtime. Recovery rates typically range between 95–98%.
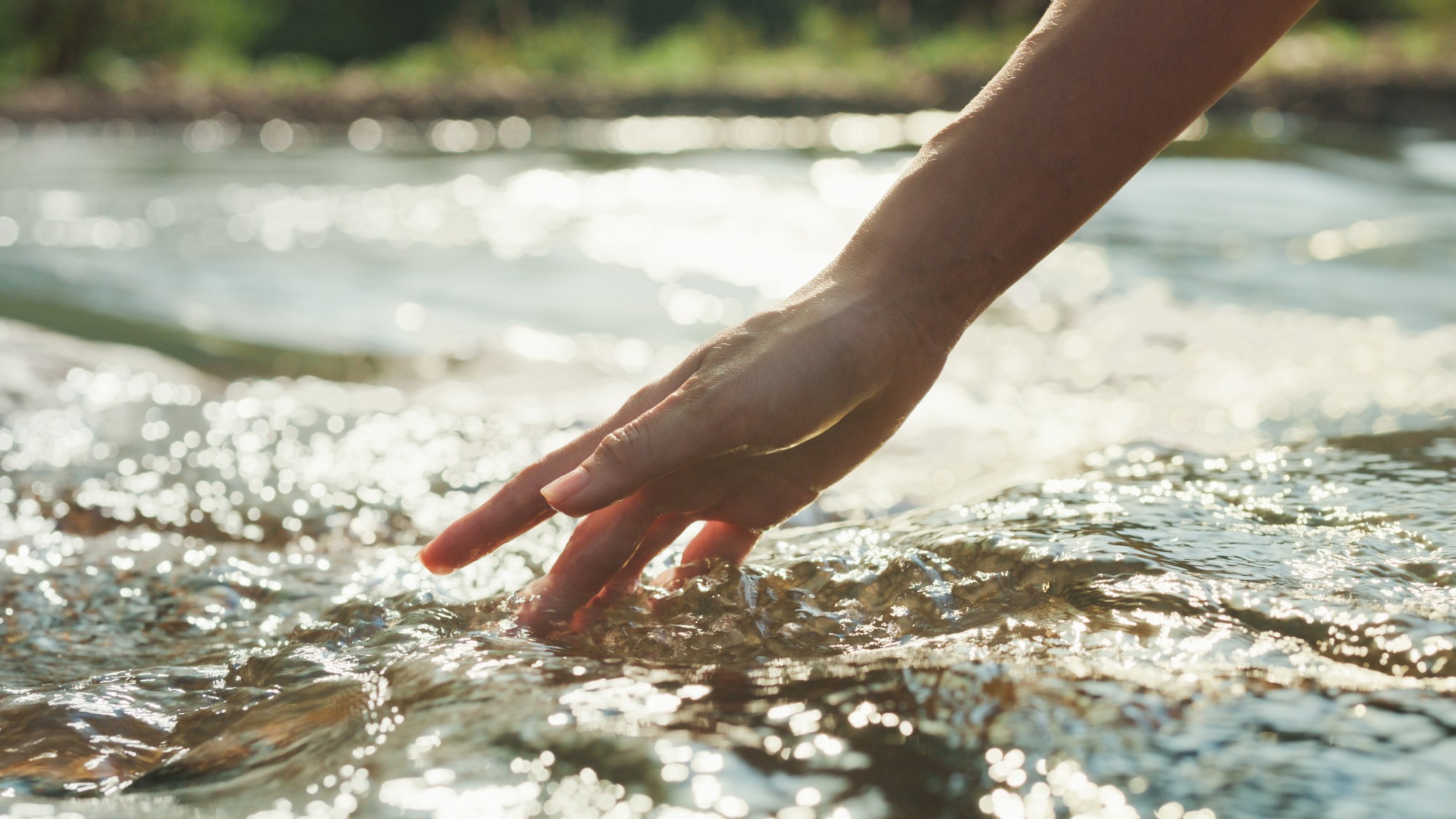
Key figures
Contact our experts
References
See all our references
- Municipal
- Municipal drinking water
Andijk III Water Treatment Plant (PWN)

- Municipal
- Municipal drinking water
Quellwasserwerk Sonnenberg (ewl)
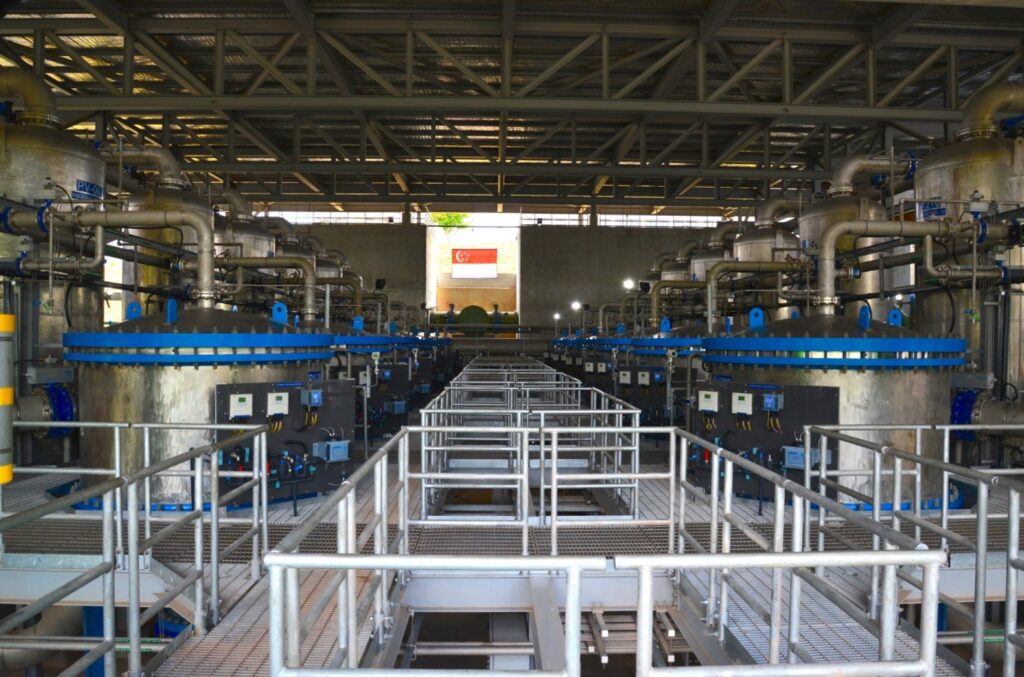
- Municipal
- Municipal drinking water
Choa Chu Kang Waterworks (PUB)

- Municipal
- Municipal drinking water
Mayflower Water Treatment Works (South West Water)
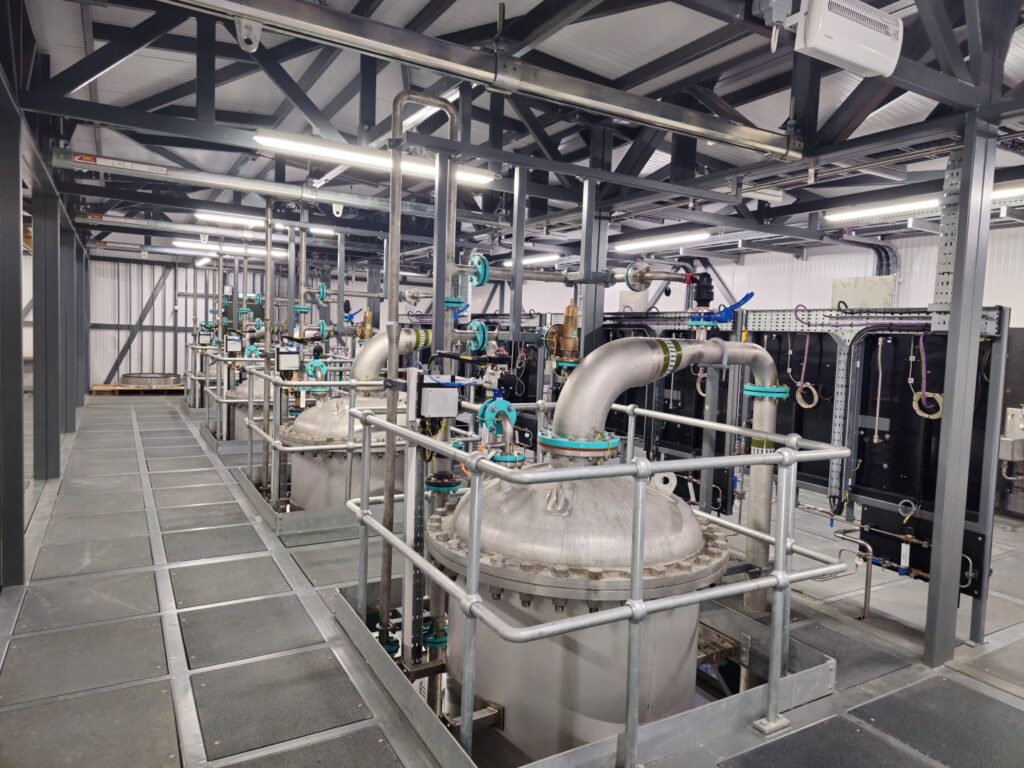
- Municipal
- Municipal drinking water
Bonnycraig Water Treatment Works (Scottish Water)
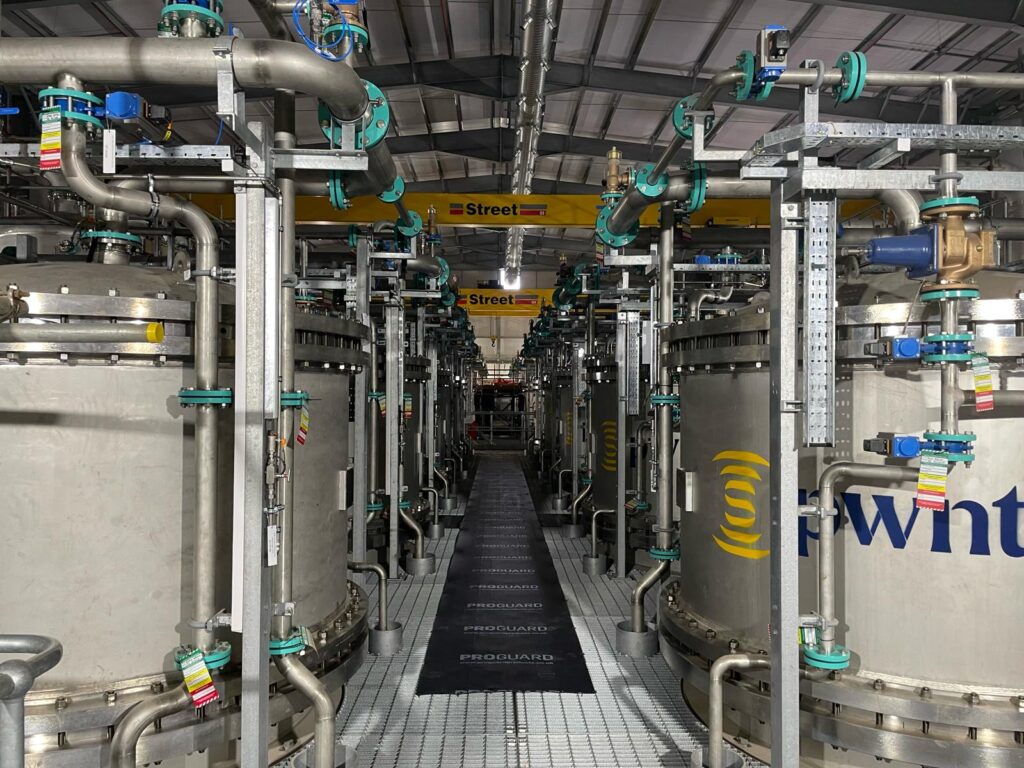
- Municipal
- Municipal drinking water
Hampton Loade Water Treatment Works (South Staffs Water)

- Municipal
- Municipal drinking water
Witches Oak Water Treatment Works (Severn Trent)
Frequently asked questions
How sustainable are the materials used in CeraMac®?
CeraMac® is built from nearly 100% recyclable materials, with no plastic. Its main components are stainless steel pressure vessels and ceramic membrane elements. Each part of the system (ceramic, steel, titanium, gaskets) is a single-material component, making separation, recycling, and disposal more efficient and environmentally responsible at the end of its service life.
What is the membrane element made of?
Each membrane element is made of aluminium oxide, an inorganic and highly durable ceramic material, with a nominal pore size of 0.1 µm and 25 m² of filtration surface area. The elements are supplied by Metawater, a leading global manufacturer of ceramic membranes.
What is the expected lifespan of the ceramic membranes?
Ceramic membranes have an indefinite lifespan, with over 20 years of proven continuous operation in real-world applications. While actual service life depends on operating conditions and maintenance, it typically far exceeds that of polymeric alternatives.
How do ceramic membranes compare to traditional polymeric membrane systems?
Ceramic membranes offer superior durability, longer lifespan, and resistance to chemical and thermal degradation. This leads to reduced maintenance and operational costs. In contrast to polymeric membranes, ceramics are inorganic, do not degrade into microplastics, and are far more sustainable over their life cycle.
How is membrane performance maintained under variations in water quality?
CeraMac® performs reliably under a wide range of raw water qualities and flow conditions. Standard fluxes range from 175 to 225 L/m²/h, with up to 300 L/m²/h achievable in ozone-enhanced systems. Pretreatment options like ILCA (In-Line Coagulation and Adsorption) help minimize fouling and maintain stable, high performance.
What are the typical applications of CeraMac®?
CeraMac® was originally developed for municipal drinking water treatment, but its robust performance also makes it well-suited for reuse applications and as a pretreatment for reverse osmosis (RO) in desalination processes.

- Industrial
- Municipal
Membrane filtration
- Process water
- Industrial water
- PFAS
- Micropollutants
- Wastewater
- Drinking water
- Source water
- Rainwater

- Industrial
- Municipal
Coagulation & Flocculation
- Industrial water
- Process water
- Drinking water
- Wastewater