Your challenges
Operators in the municipal and industrial sectors must improve performance within existing footprints.

Limited capacity under rising flows
When flows rise, conventional primary clarifiers and screens have trouble keeping up, which results in bottlenecks and expensive plant extensions. Without constructing more tanks, you must take a pre-treatment step that frees up space in the biological stage.
Reusing wastewater
You wish to remove suspended particles from contaminated water streams so they can be used again.
Cost reduction
Wastewater treatment can be very expensive, but you need to keep costs low. The subsequent stages of treatment are more economical when suspended particles are eliminated from sewage or industrial effluent.
High energy use and carbon footprint
One of the biggest energy users on the property is aeration. An excessive solids load raises running expenses and blower demand. The quickest method to lower energy use and CO2 emissions is to cut that load upstream.
Do you want to know more about IntenSieve®?
How does it work ?
Our process
Feed water enters the enclosed stainless-steel frame and flows onto a continually moving filter belt (90-2000 µm). As a thin cake builds, it acts as a dynamic pre-coat that sharpens separation efficiency. Belt speed automatically adjusts to water level. The filtrate (free water) passes through the mesh; captured solids travel upward, dewater by gravity, and are released by a gentle air blow-off into a discharge hopper. A cyclic hot-water rinse removes grease to keep pore openings from the filter mesh clean.
The sieve part (sieve table) of each Intensieve® can be removed easily and placed in a frame. Among other things, the filter frame is raised out of the frame to replace the sieve cloths.
Modular units (CT-80 to CT-170) can be combined to treat 5 – 50000 m₃/h and are available as plug-and-play skids for pilot or permanent use.
Our positive impact
IntenSieve® turns primary screening into a high-value capacity and resource booster.
More capacity, smaller footprint
Removes 40 – 60 % of suspended solids and 25 % of COD before biology (depending on characteristics of influent), delivering roughly 15 % total plant capacity gain without civil works.
Lower energy and carbon
By cutting solids load, aeration energy drops (~25 % for sewage treatment).
Chemical-free, low-maintenance operation
The stainless steel belt, low-pressure air cleaning, and periodic hot-water rinse keep the system clog-free without flocculants, minimizing OPEX and sludge volumes.
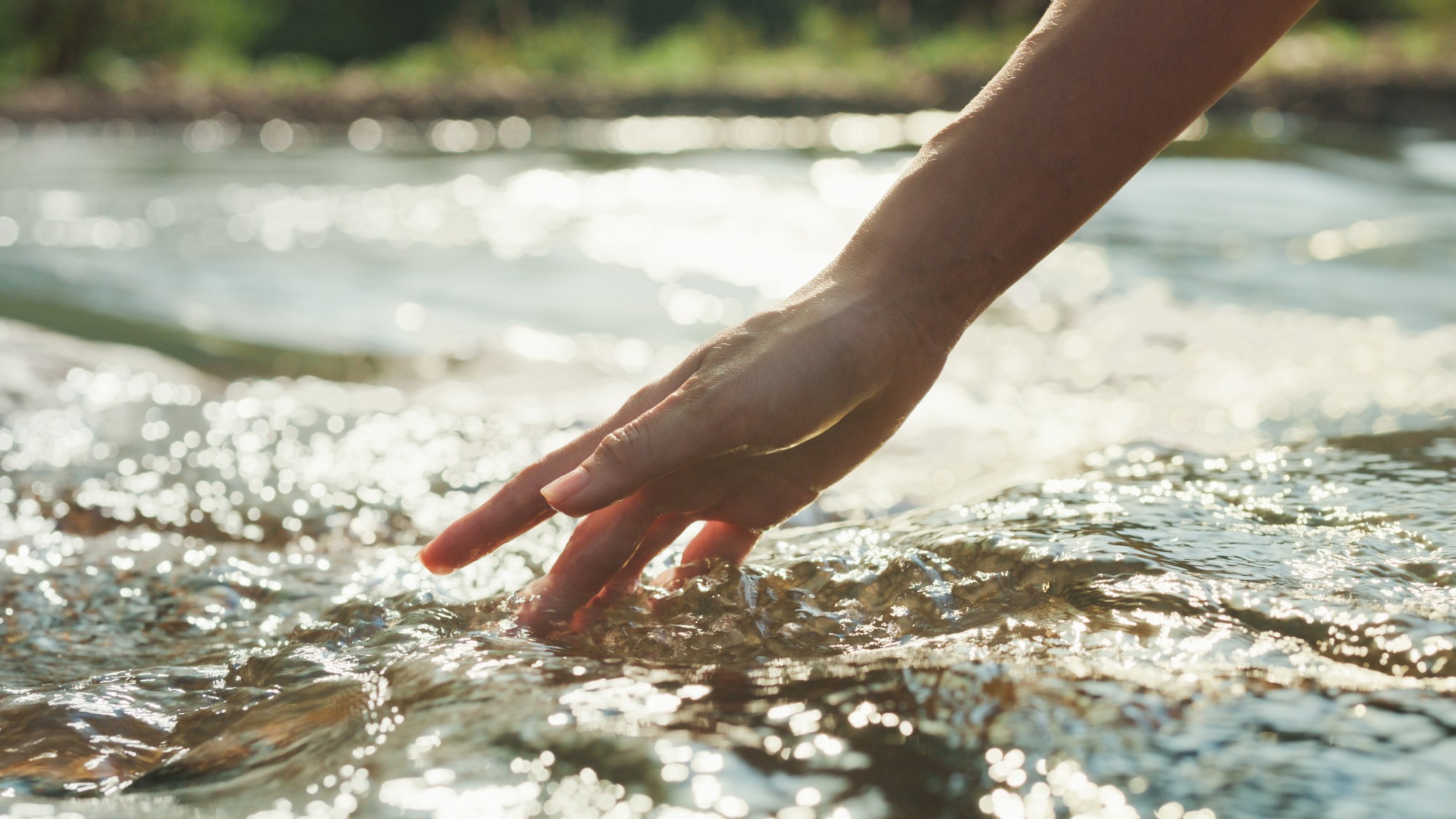
Key figures
"The IntenSieve® finesieve frees capacity, recovers resources, and shrinks energy bills - a proof that smart screening can drive #missionwater. "
References
See all our references
- Industrial
- Fish processing
Searious Fish Leather Tanning Project
Contact our experts
Frequently asked questions
What sets IntenSieve® apart from step or drum screens?
IntenSieve® combines sieving and thickening in one compact unit, achieves finer cut sizes, and delivers a drier, easy‑to‑handle fiber cake without chemicals.
Which mesh sizes are available?
Standard belts are available from 90 to 2,000 µm; we help you select the optimum size based on the solids profile and capacity targets.
Is it possible to integrate IntenSieve® with my current headworks?
Yes. Compact skid designs fit into existing channels or containers, and mobile test units allow proof‑of‑performance before full‑scale installation.
What regular maintenance is necessary?
Apart from periodic inspection, the belt is self‑cleaning via low‑pressure air and hot‑water rinse. Bearings are sealed‑for‑life, and sieve panels can be swapped in minutes.